I finally feel like I've started making progress again. I finished the engine controls, the aileron linkage and position sensor, and the brake master cylinders. I got started on the elevator position sensor but need to solve for the centering springs before I can do much more on that. The elevator linkage is easy enough since the stock Cessna linkage lends itself perfectly to the task, so it's just a matter of integrating centering springs into it.
For the elevator and aileron controls, and perhaps later the rudder pedals, I'm hoping the centering springs are only a short term need, as I have started to save pennies for force feedback. I've already made accommodations for the force feedback linkage in what I just installed for the elevator and aileron controls, but I haven't quite figured on how to integrate it into the rudder pedals yet. Ideas are stirring but nothing solid yet...
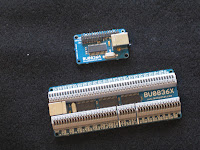
I've been bogged down for a while now trying to find viable connectors for my older Leo Bodnar BU0836A card. Bodnar's site has shown the connector as out of stock for several months now. I can only assume that, even though it's still available, with the board being superseded by the BU0836X that Leo has no intent of supplying the connectors any longer. I tested a half dozen different connectors including some that other seemed to have been able to use on their cards. I finally gave in and bought a replacement BU0836X. The "A" card won't go to waist as I will continue to use it for prototyping and may add it to the desktop pit. The new card is larger, but has wire connectors mounted on the board so that'll make the install so much easier.
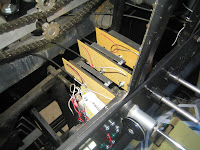
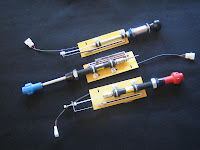
So, you saw the initial build on the engine controls in an earlier post. The only remaining step was to wire the pigtails. I decided to put 3 pin connectors on the pigtails to make things a little easier for future maintenance. With that done I installed them this past weekend.
I did run into a minor clearance problem between then and the Aileron linkage but was able to solve that easily. The spacing is a bit tight between the controls and to the right the landing gear switch, to the left the sson to be built flap switch. The flap switch may prove to be a bit more challenging given the tight space but should still be workable.
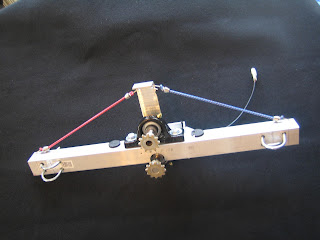
The aileron crossbar mounted easily and other than having to take an additional link out of the chain to raise it up another 1/2" and resolve the above mentioned clearance problem it dropped in as planned. The setup consists of a cross bar that mounts with u-bolts to the Cessna yoke Y-bar uprights. Centered on the cross bar are two bearing pillow blocks with Cessna yoke sprockets on 1/2" shafts. The upper has the return springs and rotation limiter bar on it. It will also be the used to connect the FFB system in the future via a universal joint on the opposite side of the bearing block. The lower shaft has a gear arrangement on
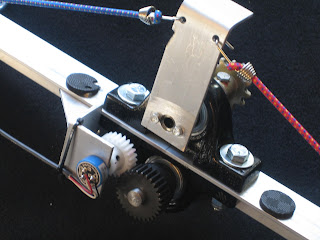
the back that connects it to the position sensing potentiometer. The gearing is setup to convert the 180 degrees of yoke rotation to 340 degrees of potentiometer rotation. Unlike that rudder or elevator linkages, that have hard stops on them, there's a potential with this aileron linkage arrangement for over torquing on the yoke to exceed the limit set by the stop arm. Because of this I chose a continuous rotation pot to eliminate the possibility of damaging a normal 340 or 360 degree pot with stops. To allow for full down elevator deflection the design required that I cut a 4" x 6" opening in the firewall.
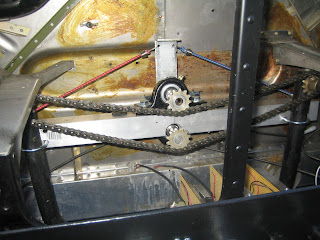
That will also be the entry point for the force feedback drive shaft at a future date. I'm not thrilled with the bungy chord arrangement for return springs but it does seem to be working. If I can come up with something better before I install the instrument panel I may be doing an upgrade. Gotta keep telling myself though that they'll be coming out as soon as I can afford the FFB system. Everything else in this portion of the install went in as designed and I'm quite satisfied with the results.
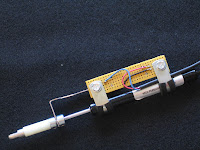
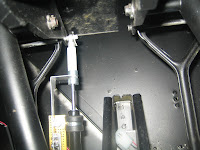
The brake master cylinders came out far better than I thought they would. I purchased some 8" mini gas springs, I did have to cut them down another 1/2" but other than that no modifications. I added a mounting board to the piston housing with a 25mm slide pot. and a linkage to the piston shaft that was held in place by a pair of shaft collars. I also installed a couple 1" spacers above that to prevent the brakes from being pushed too far and damaging the slide pots. While the design is simple, and the build was easy, installing them reminded me again why I will never be a General Aviation mechanic. I am convinced that to qualify as an A&P mechanic you need a second wrist and elbow in each arm and hands as small as a chipmunks paws. They did eventually go in, but that was after scraping a little flesh off my hands and the application of some colorful language.
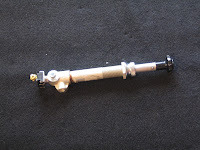
I also decided to replace the electrical switch I had put in as a dual function fuel pump and primer switch with an actual fuel primer. All I had to do was drill out the back end and fit a momentary push button switch in it. While that solves for a more realistic primer, it does leave me looking for another fuel pump switch for emulating newer aircraft. Space on the lower instrument panel is getting tight, but there is some space left. While as planned it is a generic sim pit I am still trying to stay as close as possible to the Cessna 172 format.
So that's where the work wrapped up this weekend. This coming week I'll be pulling out the wiring nail board again to retrofit it with the new bodnar card to the wire harness with the hope of getting it installed next weekend or the weekend after.